Ball valves are essential components in fluid control systems, used across industries like oil and gas, water treatment, and chemical processing. Known for their high durability, precision control, and ability to withstand extreme pressure and temperature, ball valves offer reliable performance in critical applications. But what exactly goes into making a ball valve? This comprehensive guide breaks down the ball valve manufacturing process step by step—from raw materials to quality control.
1. Raw Materials Selection: Laying the Foundation for Durable Ball Valves
The first and most important step in the ball valve production process is selecting the right raw materials. Material quality directly impacts the valve’s durability, corrosion resistance, and pressure-handling capabilities.
- Stainless Steel: Ideal for high-pressure applications and corrosive environments like marine, oil and gas, and chemical industries.
- Brass: Common in residential plumbing and HVAC systems due to its resistance to corrosion and affordability.
- Bronze: Offers excellent wear resistance and is often used in marine environments.
- Plastic (PVC, CPVC): Suitable for low-pressure, non-corrosive systems like irrigation or water filtration.
Each material is carefully inspected for quality and compliance with industry standards before entering production.
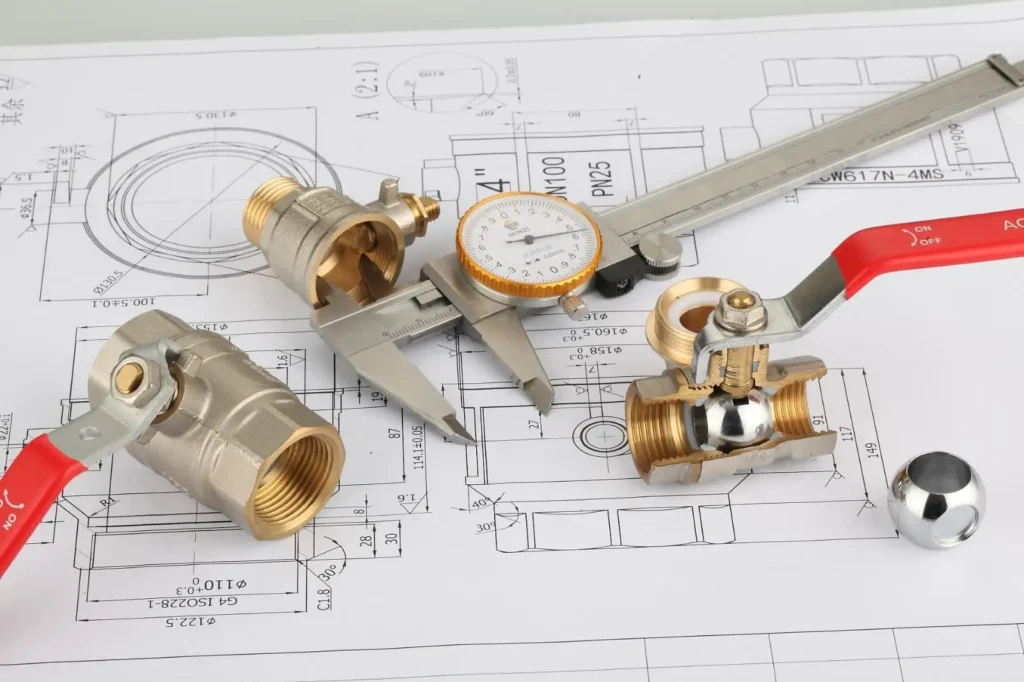
2. Casting or Forging: Selecting the Right Manufacturing Technique
Once materials are selected, the next step is shaping the valve body. Manufacturers choose between casting and forging, depending on the application and performance requirements.
- Casting involves melting the metal and pouring it into a mold to create complex shapes. It’s ideal for intricate designs with internal channels or delicate features.
- Forging shapes the metal using pressure and heat, which aligns the grain structure and strengthens the material. Forged ball valves are preferred in high-pressure and high-temperature industrial systems because of their superior durability and fatigue resistance.
The method chosen plays a key role in the final valve’s performance and life expectancy.
3. Shaping the Valve Body: Precision Machining for Maximum Performance
After casting or forging, the valve body is machined for dimensional accuracy. This ensures the smooth flow of liquids or gases through the ball valve and prevents leaks.
- CNC (Computer Numerical Control) machining is used to cut precise threads, drill holes, and form sealing surfaces.
- Internal surfaces are polished or coated to reduce wear and improve flow efficiency.
- All parts must meet strict tolerances to ensure seamless assembly later in the process.
Precision in this step is critical to the valve’s ability to operate under high pressure and withstand repeated use.
4. Component Assembly: Building the Complete Ball Valve
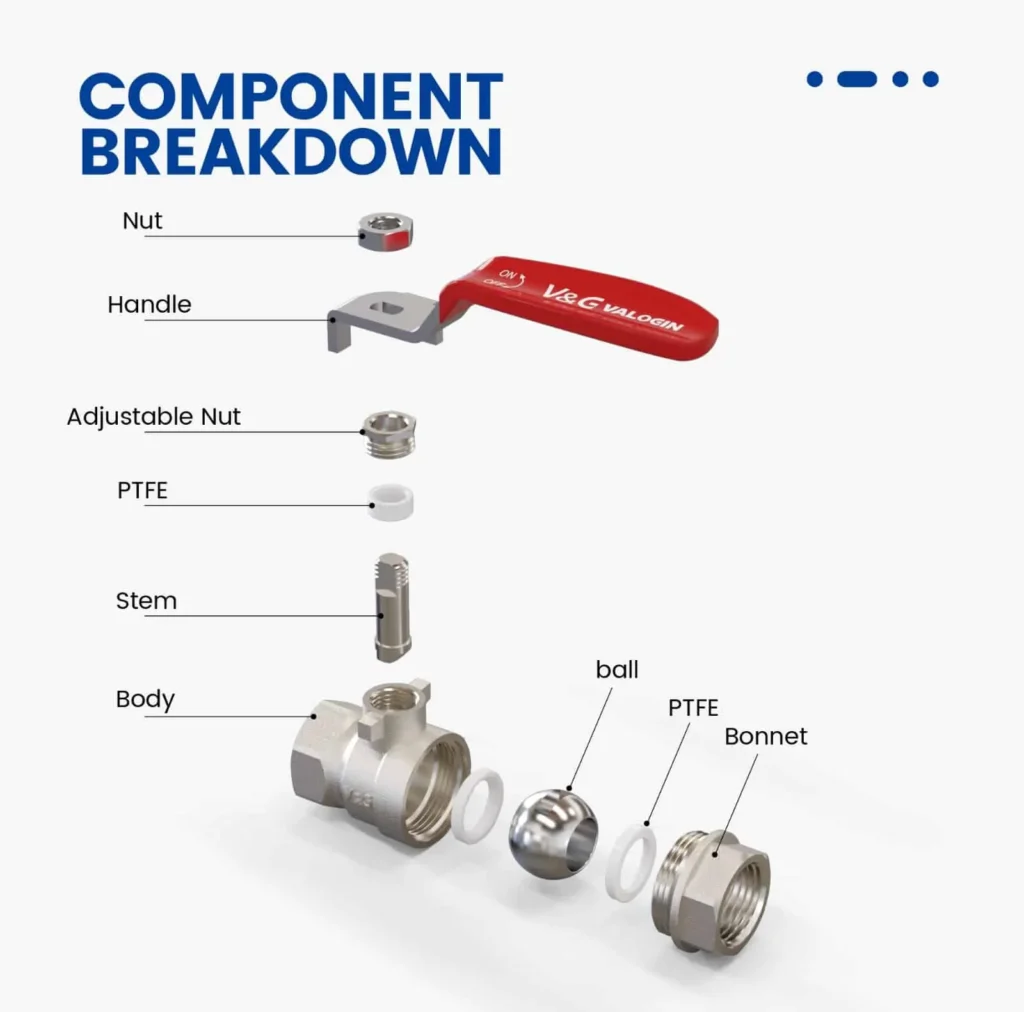
The next phase is assembling all internal and external components of the ball valve. This includes:
- Ball: Usually made of stainless steel or chrome-plated brass; it controls flow by rotating inside the valve.
- Seats: These are often made from PTFE or other polymers, creating a tight seal when the valve is closed.
- Stem: Connects the ball to the handle or actuator.
- Seals and Gaskets: Prevent leakage around the stem and body joints.
Skilled technicians assemble each part manually or with semi-automated tools. Some valves may also include handles, gearboxes, or pneumatic/electric actuators depending on the use case.
5. Quality Control and Testing: Ensuring Safety and Reliability
Every ball valve must pass a series of rigorous quality assurance tests before shipping. These include:
- Hydrostatic Pressure Testing: Ensures the valve holds pressure without leaking.
- Air Leakage Testing: Checks for leaks under low-pressure conditions.
- Torque Testing: Verifies that the ball rotates correctly with proper effort.
- Dimensional Inspection: Confirms that all parts meet design specifications.
In addition to performance testing, valves undergo cleaning, deburring, surface finishing (anodizing or coating), and anti-corrosion treatments. Final inspection includes labeling, packaging, and documentation to meet ISO and industry standards.
Conclusion: The Value Behind Precision-Crafted Ball Valves
The ball valve manufacturing process involves a detailed series of operations designed to ensure performance, safety, and longevity. From selecting corrosion-resistant raw materials to precision machining and strict quality control, each step plays a crucial role in the final product’s efficiency.
Whether for industrial, commercial, or residential applications, a well-manufactured ball valve guarantees smooth fluid control, leak resistance, and long-term reliability. Understanding this process helps engineers, buyers, and end-users make informed decisions when selecting ball valves for specific needs.
2 Comments
Hayesplumbing
August 8, 2023This in-depth article on the manufacturing process of ball valves offers valuable insights into the world of industrial production. As someone curious about engineering and manufacturing, I found this behind-the-scenes look fascinating. The precision and attention to detail required to produce high-quality ball valves are commendable. Understanding the craftsmanship and effort that go into creating these essential components enriches our appreciation for the mechanics behind everyday items. It’s inspiring to learn about the dedication of professionals in the valve manufacturing industry, ensuring reliable and efficient products for various applications.
zoritoler imol
November 27, 2023I just wanted to make a simple word to be able to thank you for some of the magnificent pointers you are giving out at this website. My particularly long internet research has at the end of the day been honored with brilliant tips to exchange with my relatives. I would mention that most of us website visitors are very fortunate to dwell in a notable community with so many perfect professionals with useful advice. I feel somewhat blessed to have discovered your entire web page and look forward to plenty of more cool minutes reading here. Thanks once more for everything.